Minimizing downtimes in the LRM segment thanks to predictive maintenance
Predictive maintenance allows LRM service providers to minimise vehicle downtime and maintenance costs by using real-time data to optimise service schedules, improve vehicle longevity, and enhance safety
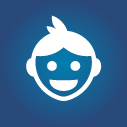
By Geotab Team
May 1, 2025
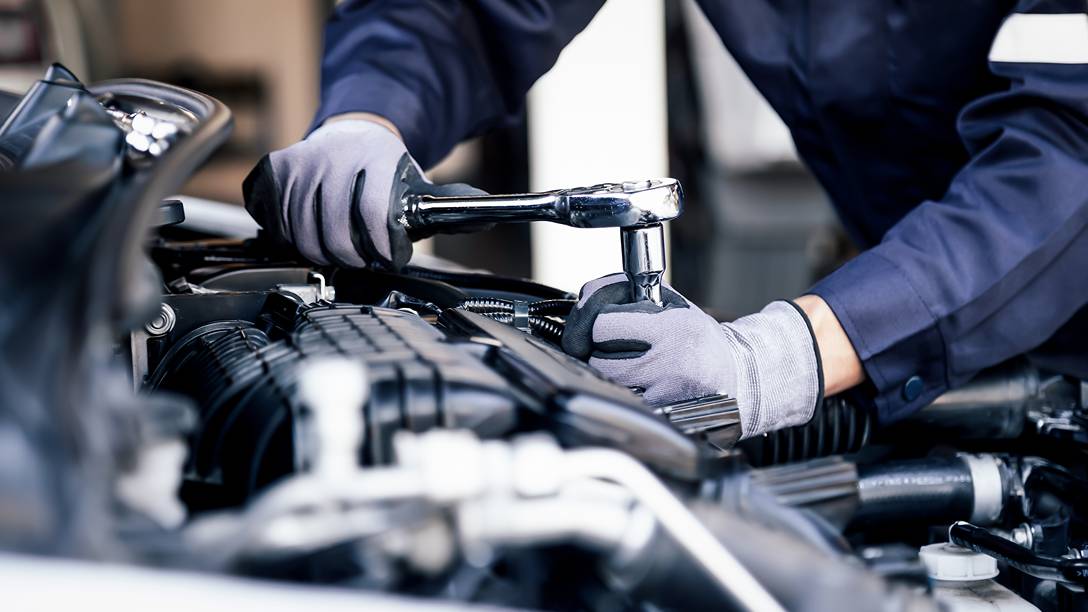
For providers of mobility services of all kinds – be it leasing, traditional car rental or innovative car-sharing services – idle vehicles have a direct negative impact on their turnover. The LRM industry (leasing, rental, mobility) therefore focuses on guaranteeing the longest possible, uninterrupted operating times for vehicles. But this must never be at the expense of safety. The safety of drivers and passengers should always be the top priority. However, the longevity and value retention of the vehicles should also be ensured. Fleet managers want to avoid excessive wear and tear in order to be able to use their vehicles for as long as possible and resell them in the best possible way.
Hidden costs due to unplanned breakdowns
If a rental car breaks down unexpectedly, there are hidden costs in addition to the obvious ones, such as repair and replacement parts. These include:
- Loss of revenue: While a vehicle is being repaired, or during the waiting time before it is repaired, it obviously cannot be rented out and therefore does not generate any revenue.
- Depreciation: Vehicles involved in accidents and requiring extensive repairs lose market value.
- Administrative burden: Claims management, communication with insurance companies and customers tie up resources and put a strain on employees.
- Loss of reputation: Customers can experience major inconvenience if they do not receive a booked vehicle or an adequate replacement is only available after a long delay. Negative reviews and even long-term customer loss can result.
- Contractual penalties: In the B2B sector, contractual penalties may be incurred if business customers or partner companies have been contractually guaranteed certain vehicle availability.
The challenge of maintenance planning
Fleet managers have to plan their vehicles' visits to the workshop in such a way that downtimes are kept to a minimum and wearing parts are replaced in good time. On the other hand, they do not want to replace expensive parts purely on spec and possibly discard components that are still intact. This so-called preventive maintenance is ultimately associated with unnecessary costs and is not sustainable. For a long time, however, this was common practice and many safety-relevant components were replaced before their time to be on the safe side. Nowadays, however, the possibilities offered by modern sensor technology make it possible to extend service lives without compromising on safety or risking excessive wear. This is exactly where predictive maintenance comes into play.
What is predictive maintenance?
Predictive maintenance uses data and analysis to predict potential failures of machines, devices and components. The concept has been around for some time, but was long considered impractical and not cost-effective because manual, interval-based data collection involves a great deal of effort. However, this has changed thanks to comprehensive digitalisation and networking, and data collection and transmission are now possible in near-real time.
Modern vehicles record a number of data points from which conclusions can be drawn about the condition of certain assemblies and parts. Based on this, further measures can be initiated. In the simplest case, for example, a tyre sensor indicates that the air pressure is too low. The driver can take remedial action and inflate their tyres (or have them inflated). However, the predictive maintenance of vehicles involves significantly more and more complex sensor data, which also allows components such as the engine and chassis to be analysed. Based on this and a comprehensive basis of comparative data, an optimum maintenance interval can be calculated for certain critical parts.
Bringing data into line
Large car rental companies can have several hundred vehicles in their fleet per location. For fleet managers, planning maintenance means a lot of work – especially as different vehicle types and brands are involved. For example, different requirements apply to small cars than to vans, and different requirements apply to petrol cars than to diesel cars. Electric cars have added another dimension in recent years. Although electric vehicles are generally considered to be easier to maintain, they naturally also have critical wear parts such as brake pads and discs. In addition, those responsible should always be able to keep an eye on the battery status.
We can assume that all these different vehicles in modern fleets collect large amounts of data during operation. In principle, this is therefore a good basis for implementing predictive maintenance. However, bringing together the data records of different vehicle types from different manufacturers is an immense task without suitable tools. If too much manual work is required, fundamentally innovative approaches may even become uneconomical.
Why a central platform is important
Telematics and data platforms play a central role in the implementation and improvement of predictive maintenance by enabling the continuous collection, transmission, aggregation and analysis of real-time data from different vehicles. Critical parameters recorded on board, such as temperature, vibration or air pressure, are transmitted via telematics systems to the central platform, where they are automatically evaluated and processed. A particular strength of these systems is their ability to harmonise data. Regardless of whether they originate from proprietary OEM data or retrofitted telematics hardware, fleet managers receive a uniform picture of their fleet. Not only does this give them a constant overview of the current status, but thanks to machine learning it is now also possible to automatically detect anomalies at an early stage and point out potential failures. On this basis, the optimum maintenance time can be precisely determined, which minimises unplanned downtimes and extends the service life of components. In addition, maintenance can be planned efficiently and in line with demand, resulting in considerable cost savings and increased system reliability.
Advantages for mobility service providers
Properly implemented and equipped with a solid data basis, predictive maintenance can bring many benefits for LRM companies:
- Avoiding long downtimes
Predictive maintenance helps to identify potential problems early before they lead to serious breakdowns. This reduces unexpected repairs and minimises unplanned downtime, thereby avoiding or at least limiting revenue losses as much as possible. - Fewer visits to the workshop
By planning maintenance measures in advance, several service jobs can be efficiently bundled. This means fewer separate workshop appointments and therefore less downtime and costs. - Improved road safety
Early detection of safety-relevant defects – such as worn brakes – reduces the risk of accidents. Fleet managers can take high-risk vehicles out of circulation at an early stage or replace them in a targeted manner. - Higher fuel efficiency
Predictive maintenance can significantly reduce fuel consumption through targeted maintenance of the engine, tyres, cooling system or other components. - Longer vehicle service life
The service life of vehicles is extended by rectifying signs of wear and tear in good time. Major repairs such as engine damage are avoided as far as possible, the investment in the fleet is maintained for longer and profitability increases.
Make your fleet fit for the future
Fleet managers who are at home in the dynamic LRM market should no longer hesitate to use their vehicle data as efficiently and productively as possible – otherwise they could be at a competitive disadvantage. Predictive maintenance is an extremely exciting approach to turning this treasure trove of data into cash – but it is by no means the only one.
Subscribe to the Geotab Blog
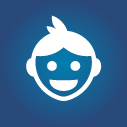
The Geotab Team write about company news.
Related posts
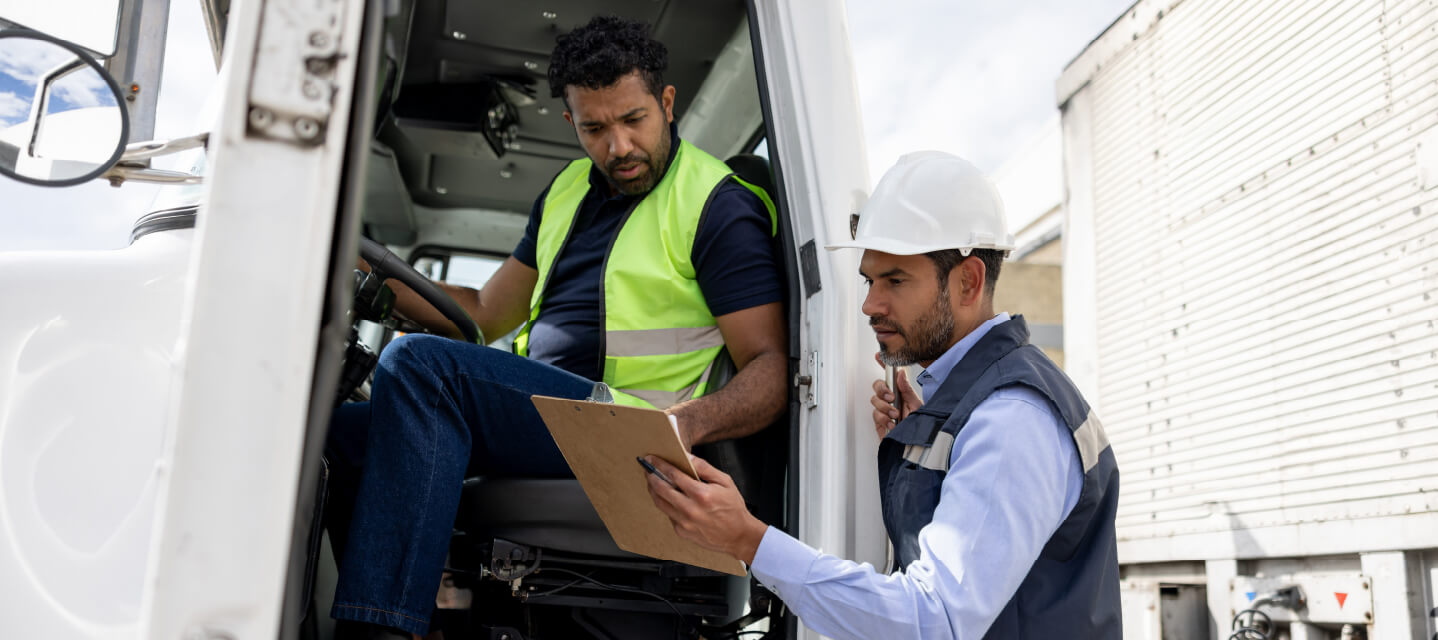
What Is fleet management? A complete guide for fleet managers
June 13, 2025
5 minute read
.png)
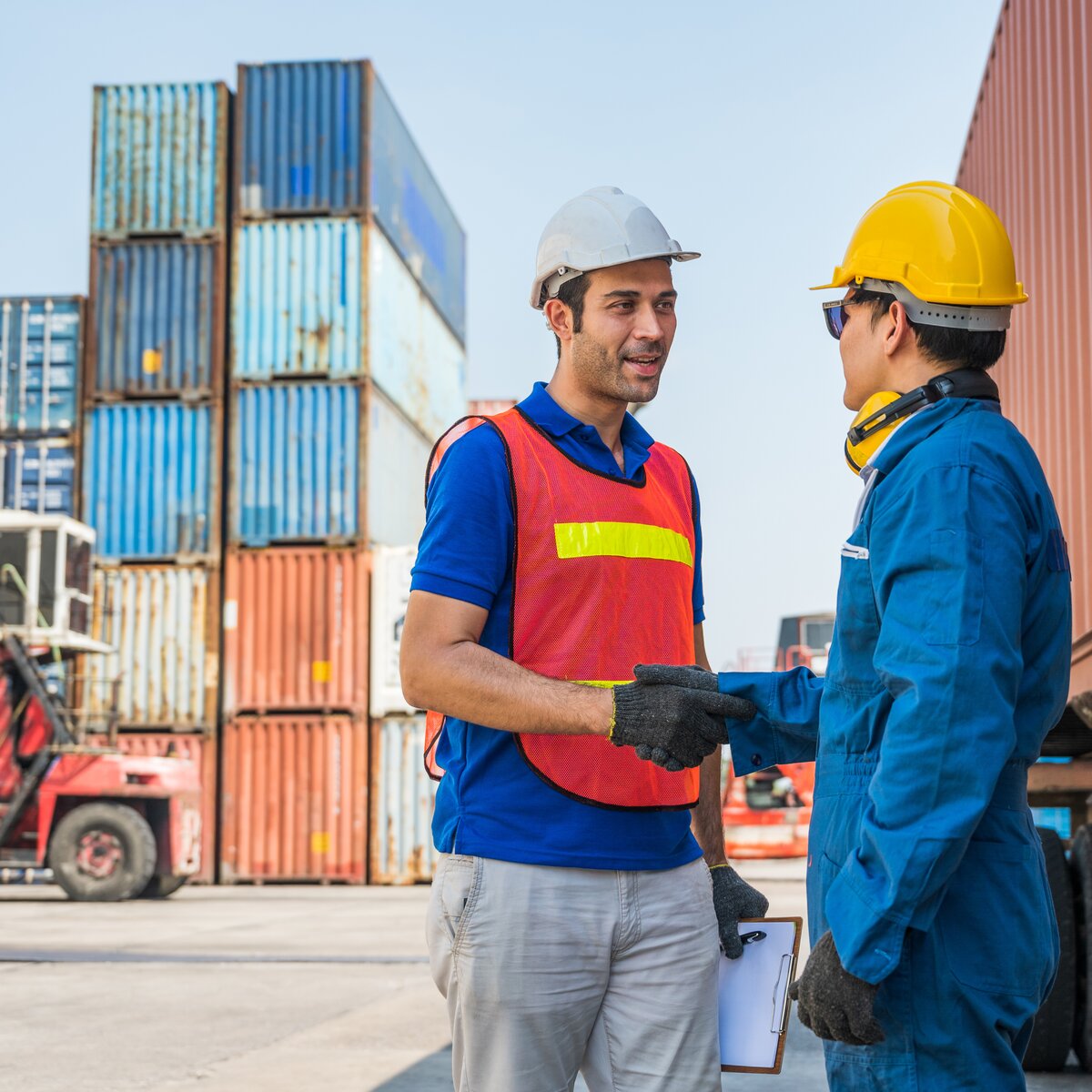
.jpeg)
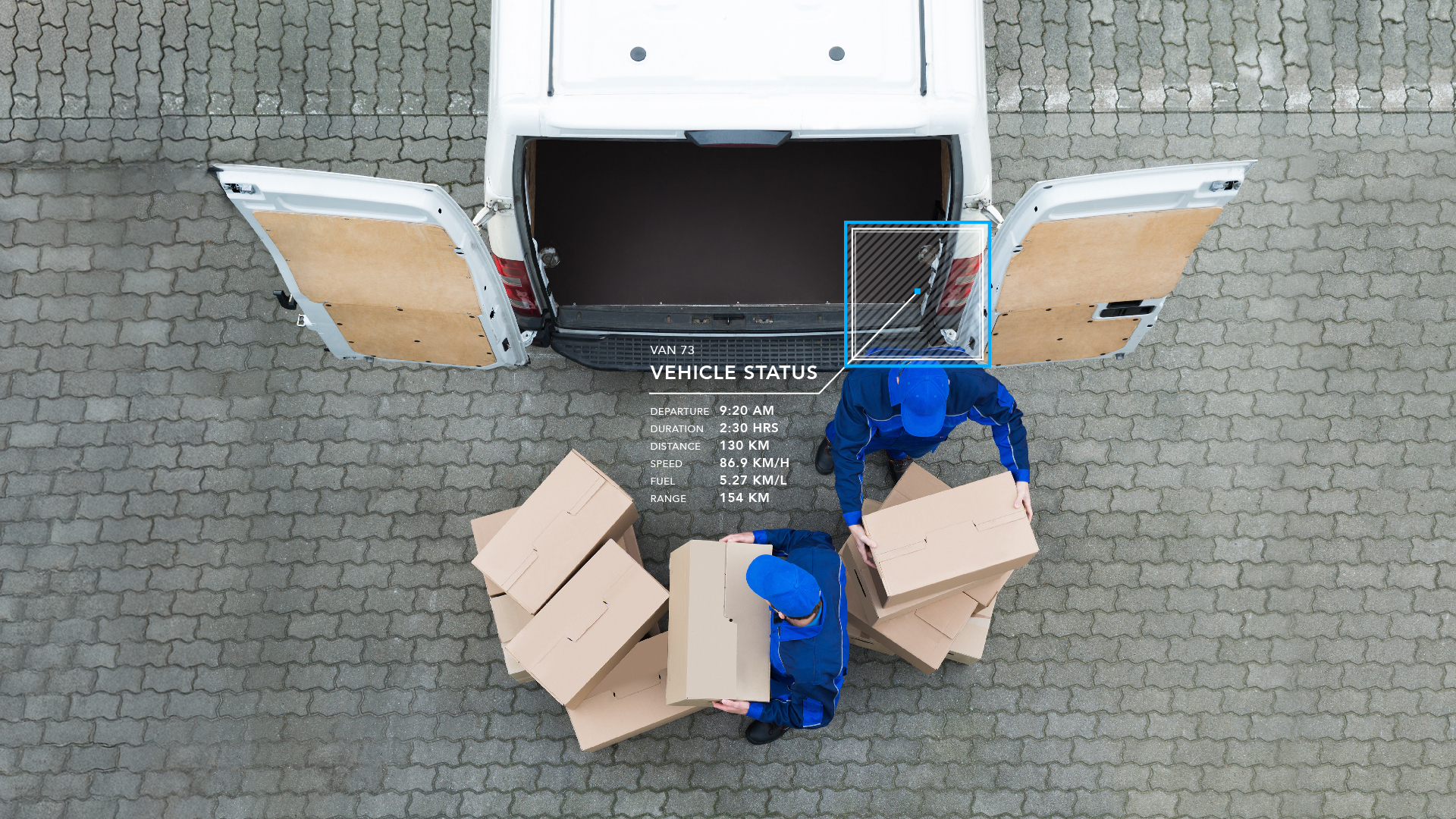
Strategic Implementation of Telematics for Optimising Last-Mile Delivery Operations
April 1, 2025
2 minute read
.jpg)