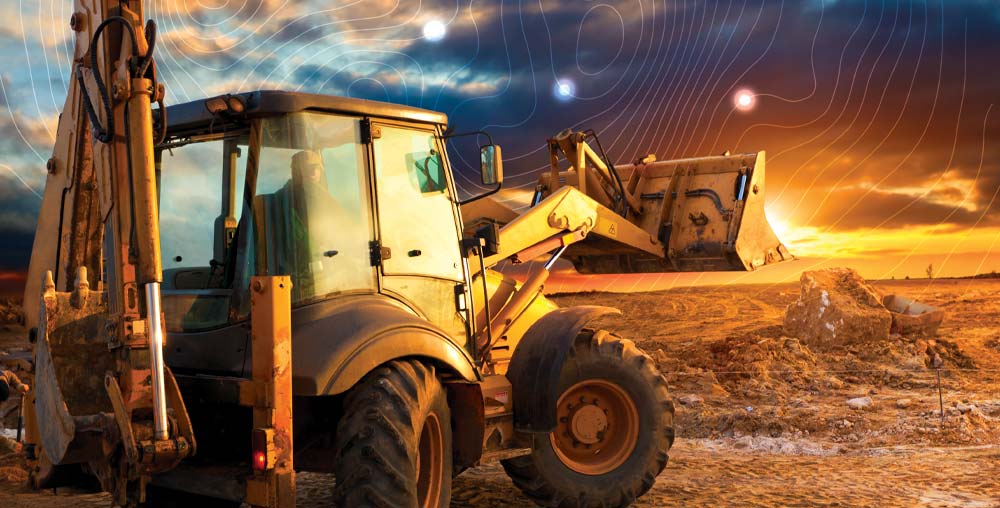
Quick guide to off-road fleet tracking
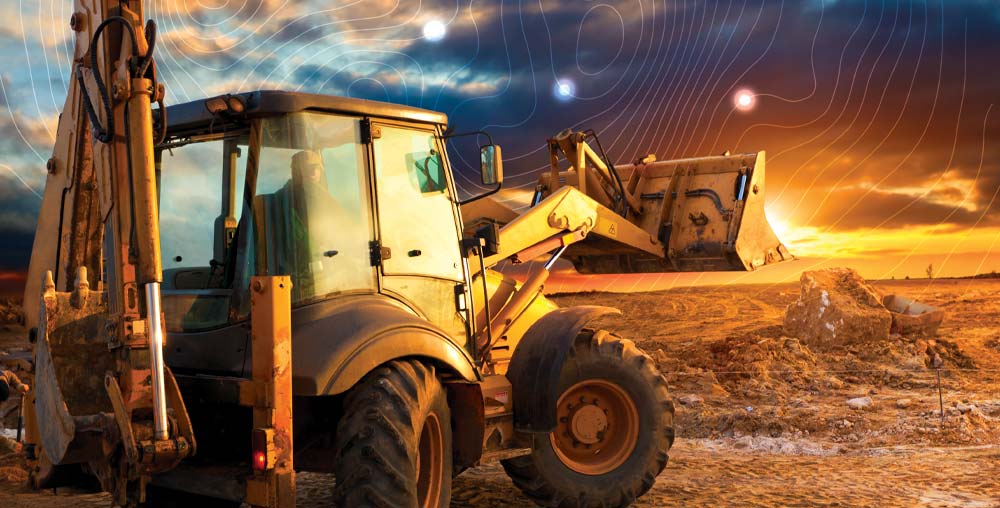
Table of Contents
Introduction
In the 21st century, manufacturing and transportation have been redefined by IoT and connectivity. For many businesses, having real-time information on quality, performance and compliance is a critical part of operations.
Similarly, the fleet world is embracing telematics and data and analytics.
- The Global Fleet Survey 2019 reports that 50% of North American fleets will have implemented telematics by 2022.
- Berg Insight predicts that the number of fleet management systems being actively used in Europe will reach over 15 million units by 2022.
- The U.S. electronic logging mandate for commercial motor vehicle drivers led to a major wave of telematics adoption. C.J. Driscoll & Associates estimates that now “97% of Truckload carriers and interstate Private fleet operators have a commercial telematics solution.” Canada is also following suit with its own ELD regulations, coming into effect in 2021.
Off-road fleets are starting to see the advantages of fleet tracking technology as well. These days, telematics is far from one-size-fits-all and offers specific solutions for heavy equipment and off-road vehicles.
This guide is designed to help business owners and fleet managers understand the essentials and learn how it can be used to benefit their own organization.
What you will learn:
- What is off-road tracking?
- How it works
- Benefits of fleet tracking
- Top use cases
- Getting started
What is off-road fleet tracking?
Off-road fleet tracking is the monitoring of an off-road asset (cranes, lifts, heavy equipment) with an IoT device that collects GPS location, vehicle speed, driving behavior, engine data, and other information.
Telematics is an important fleet management tool, not only for transportation and logistics companies, but also for fleets in construction, agriculture, utilities, and oil, gas and mining. Rental fleets and vehicle and equipment manufacturers are increasingly making use of telematics. Developments in satellite and cellular communications have made it possible for telematics devices to work even when vehicles are out on remote worksites.
Definitions to know
Geofencing: Creating geographic zones within telematics software to set up boundaries and track activity at specific places. Common types of geofences or zones include an office or customer location.
GPS algorithm: The process that instructs how GPS data (position and time) is logged onto the server. Algorithms may vary among telematics providers.
IP standard: The IP code is an international standard for classifying the ingress protection rating of devices, or how resistant they are to contact, dust, and moisture, etc. The digits after the letters “IP” indicate or the level of protection it provides against intrusion of solids and liquids.
Open platform: A flexible telematics system which provides open or free access to the data through a software development kit (SDK) and application programming interfaces (APIs), in contrast to a closed platform in which access to data is limited or filtered.
Telematics: The use of GPS, telecommunications technology, sensors and the internet to monitor connected vehicles and equipment. Telematics is another term for off-road fleet tracking.
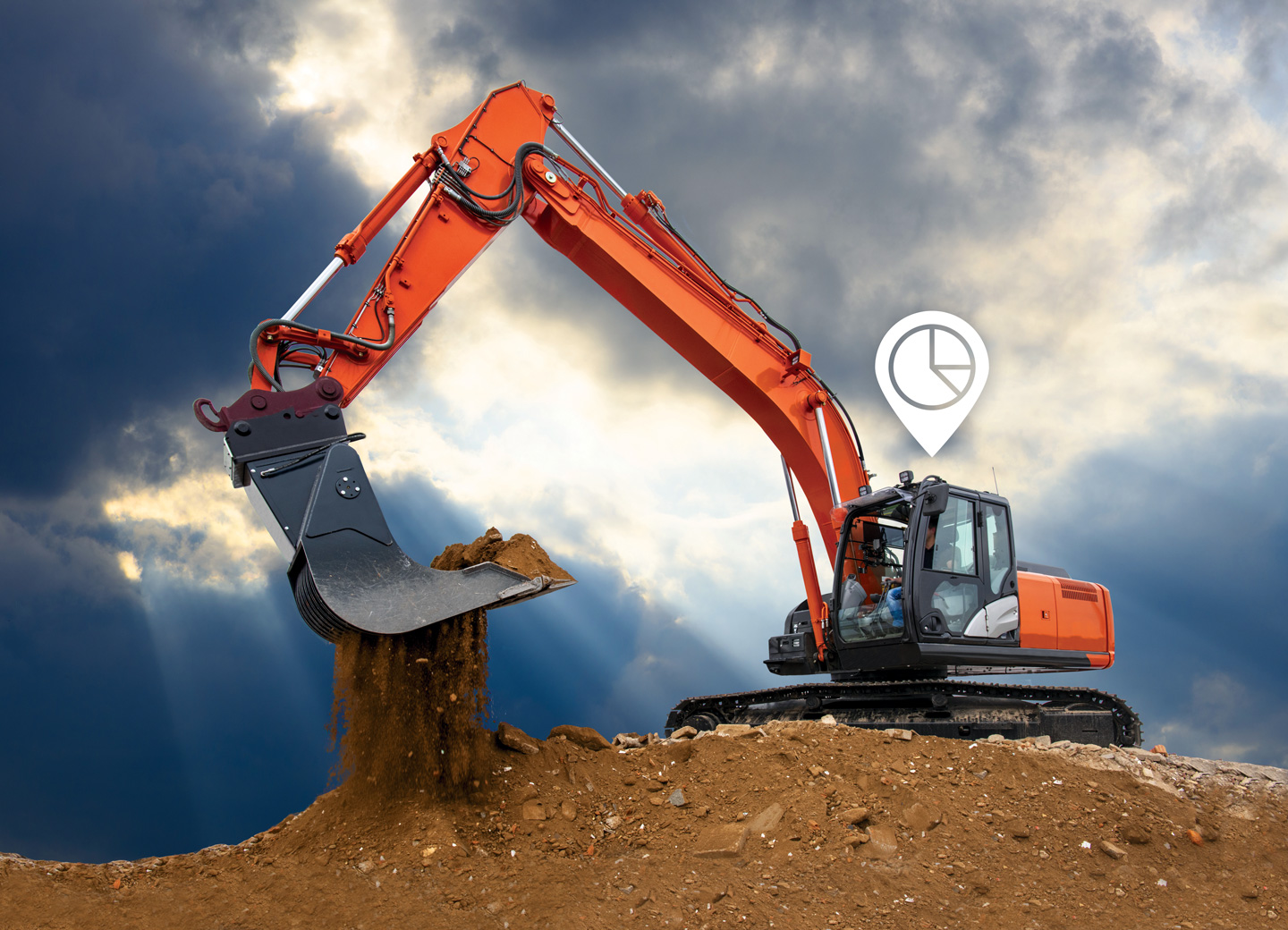
The connected off-road fleet
Fleets can use off-road telematics in many different ways.
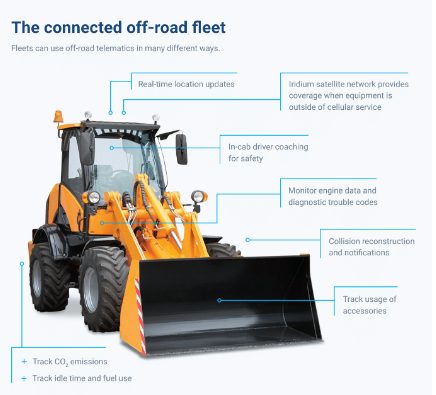
- Monitor engine data and diagnostic trouble codes
- Track idle time and fuel use
- Track usage of accessories (plow-down, bucket-up, etc.)
- Real-time location updates
- In-cab driver coaching for safety
- Collision reconstruction and notifications
- Track CO2 emissions
- Iridium satellite network provides coverage when equipment is outside of cellular service
Types of vehicles/equipment:
- Heavy-duty trucks
- Heavy machinery
- Off-road vehicles
- Aerial access equipment
- Material handling equipment
- Yellow iron, earth-moving equipment and excavators
- Mining equipment
- Big loader dump trucks
- Airport ground support equipment
- Vehicles or devices without an interior cab
- Trailers
- Generators
- Pumps
How it works
A telematics solution is made up of a combination of hardware and software, including the telematics device, harnesses and fleet management software.
The telematics device is plugged in or connected by harness to the off-road vehicle or equipment and transmits GPS position, speed and other vehicle and driving data to the cloud, which is then brought into the fleet management software system for viewing and reporting.
Not all telematics solutions are the same. There are basic trackers with limited functionality, and then open platform type solutions including a software development kit and online marketplace. Expandable telematics systems are ideal for fleets interested in connecting more apps or accessories like cameras; requiring satellite coverage; wanting to integrate telematics data with other business systems; or needing extra flexibility and scalability.
Key components of an off-road telematics solution
Ruggedized telematics device
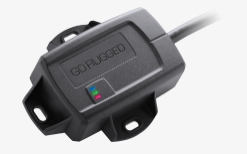
For off-road applications, involving heavy equipment, yellow iron, powered trailers and other assets where dust, dirt, snow or water are a factor, an IP67 rated device that is designed for harsh conditions or external installation is recommended over a standard device.
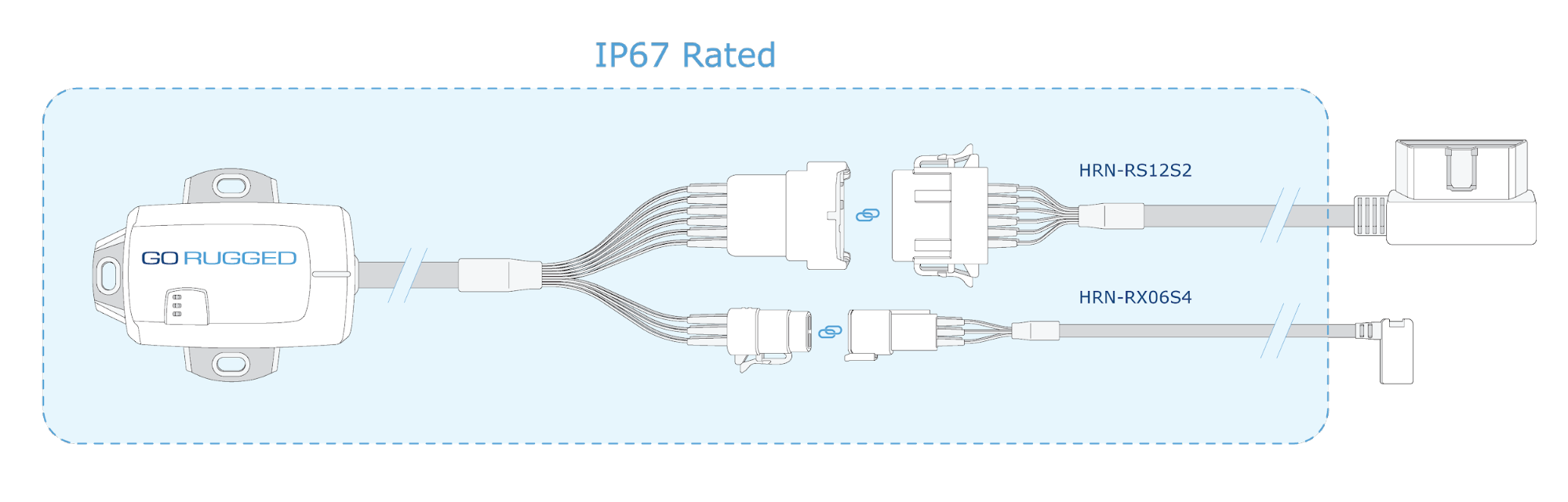
Diagram of the scope of the IP67 rating on the Geotab GO RUGGED device.
Fleet management software
.png)
The fleet or safety manager can monitor fleet trends and reports from their computer, smartphone or tablet. Custom rules and alerts can be set for harsh braking, idling, entering and exiting zones, or activities requiring management.
App store
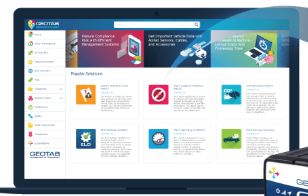
Similar to smartphones, telematics systems can be customized by adding on third-party hardware or apps from an online marketplace of integrated fleet solutions. Some examples of solutions that can be added on are satellite coverage, worker safety systems, tire pressure monitoring or a driver scorecard.
Why telematics?
Fleets with off-road vehicles and heavy equipment can use telematics for many different purposes. In general, knowing where equipment are located and what they are doing are primary benefits. Telematics can also help increase efficiency and driver safety, improve equipment utilization, reduce downtime and cut operational costs.
Overall, telematics can make life easier for the busy fleet manager by providing a centralized place for tracking and managing assets and saving time related to administrative activities, with dashboards, automated reporting and email or text alerts.
Benefits of off-road fleet tracking
Productivity
- See the location of equipment
- Improve equipment utilization
- Increase uptime
Fleet optimization
- Keep equipment in good running condition with maintenance tracking and scheduling
- Increase speed of service calls with location and diagnosis information (remote troubleshooting)
Customer service
- Know exactly where equipment assets are, for more efficient pick-ups and deliveries
- Improve accuracy of job estimates and billing
Cost management
- Improve resale value with detailed records of use
- Reduce excessive fuel use and idling
- Reduce labor costs and overtime
- Possible insurance premium savings
Safety
- Minimize unsafe use of machinery
- Monitor tire pressure and temperature
- Reinforce safe driving and seat belt use
- Gather collision reconstruction data for insurance and training purposes
Security
- Assist in recovering stolen equipment
- Know when vehicles are taken off the job site with geofencing and alerts
Top use cases for off-road fleet tracking
One of the notable characteristics of telematics is that it can be tailored to different applications. The same system can be used for simple tasks like tracking location, or for larger projects, such as understanding trends, such as on fuel and utilization and making improvements. The use cases for telematics are very numerous, especially with an open platform system that makes it easy for fleets to customize the solution to their own business by adding in third-party apps or hardware.
To better illustrate how off-road fleet tracking is used, here are some specific industry examples.
Construction
Construction machinery and equipment are specialized. Ensuring that these valuable assets are properly operated, maintained, and monitored is critical in order to maximize their efficiency and minimize the amount of unnecessary costs that must be added to a project.
The fact that assets are high value and often working in remote locations makes them easier targets for theft.
Types of questions asked by construction fleets:
- Is there too much equipment on site or not enough?
- Is one machine doing too much work compared to others?
- Is a machine sitting idle too long?
Challenge: A fleet has three backhoes on one job site and wants to measure how many hours the equipment is running in order to optimize equipment utilization.
Solution: Track equipment location, state of operation and engine diagnostics. Set up specific rules around expected hours of operation and areas of activity.
Result: By monitoring hours of usage, the fleet learns that two of the backhoes are being utilized four hours a day, but the third is only being used for two hours a week. The fleet manager determines that there is too much equipment at this job site and the third backhoe is moved to a different job site where it can be better utilized, reducing operating costs.
Off-road truck and equipment rental
For companies that rent off-road vehicles and equipment, maximizing uptime and providing great service is key to cultivating loyal customers that keep coming back. The rental industry is competitive. Creating efficiency gains and finding ways to improve the customer experience can make a big difference to profitability.
Challenge: Streamline the maintenance process and minimize customer disputes by obtaining accurate information for billing.
Solution: Track equipment usage and fuel consumed to be able to charge appropriately. Plus, schedule and report on maintenance services and repairs.
Result: With telematics data, the rental company can precisely track equipment usage for more accurate billing and transparency to customers. Armed with objective data, customer service representatives are better able to respond and resolve arguments over usage.
Now, the rental provider can look into offering flexible billing options, such as billing by hours used or a combination of time on rent plus hours used. By tracking hourly usage instead of by the day, the provider can set time limits and initiate overtime billing.
Active diagnostic faults and other engine-derived information is used to prioritize vehicles in need of maintenance. The service team can schedule preventative maintenance when it’s convenient to the customers and the rental branch. As well, instant alerts when faults occur help speed response and minimize the downtime window.
OEM
Embedded telematics is a trend that is becoming more widespread among original equipment manufacturers (OEMs). Adding a telematics device to a new vehicle or piece of equipment before it is sold to the customer has pre-sales and post-sales benefits. With consent, telematics data from the manufacturer can be integrated into the fleet management platform via API exchange.
Challenge: Gather additional feedback for product development and support customer service.
Solution: Install a telematics connection in new vehicles at the factory.
Result: Having the ability to track vehicle performance data post-launch provides valuable insight for continuous improvement and product design. In production, telematics data is consulted for quality, so issues can be resolved at the factory, before they become greater problems out in the field. Improving quality reduces recall and rework, which can help provide cost savings.
Improved root cause analysis, product monitoring and alerts, allows the OEM to provide enhanced support to distributors and customers alike. Having this data also allows for more accurate warranty coverage. The OEM will have the knowledge and hard data to make warranty decisions.
Getting started
Before getting connected, a good first step for any fleet is to develop a telematics strategy. Ask: What is the number one goal to be achieved? Is it tracking the precise location of vehicles or combatting theft? Put numbers to those goals so they can be measured. If available, use existing data as a benchmark to track progress.
Taking the time to identify the exact business problems to be solved will inform hardware and accessories decisions, and make it easier to build the best fleet management solution. In addition, focusing on one or two clear goals at the beginning can help prevent overwhelm, as telematics provides access to a lot of information.
Once initial goals have been achieved, build on success by setting new targets. Engage drivers and operators in the fleet tracking program by sharing goals and results.
Conclusion
Telematics is an increasingly popular tool for fleet management. On-road fleets are already familiar with the benefits. Now off-road fleets are seeing the appeal of telematics due to its versatility and richness of data available.
Geotab as an industry-leading platform that is flexible enough to accommodate these various applications.
About Geotab
Geotab is a global leader in connected vehicle and asset solutions, empowering fleet efficiency and management. We leverage advanced data analytics and AI to transform fleet performance, safety, and sustainability, reducing cost and driving efficiency. Backed by top data scientists and engineers, we serve over 55,000 global customers, processing 80 billion data points daily from more than 4.7 million vehicle subscriptions. Geotab is trusted by Fortune 500 organizations, mid-sized fleets, and the largest public sector fleets in the world, including the US Federal Government. Committed to data security and privacy, we hold FIPS 140-3 and FedRAMP authorizations. Our open platform, ecosystem of outstanding partners, and Marketplace deliver hundreds of fleet-ready third-party solutions. This year, we're celebrating 25 years of innovation. Learn more at www.geotab.com and follow us on LinkedIn or visit Geotab News and Views.
© 2025 Geotab Inc.All Rights Reserved.
This white paper is intended to provide information and encourage discussion on topics of interest to the telematics community. Geotab is not providing technical, professional or legal advice through this white paper. While every effort has been made to ensure that the information in this white paper is timely and accurate, errors and omissions may occur, and the information presented here may become out-of-date with the passage of time.
Recent News

Combating rising fuel prices with fuel performance incentives
April 28, 2022
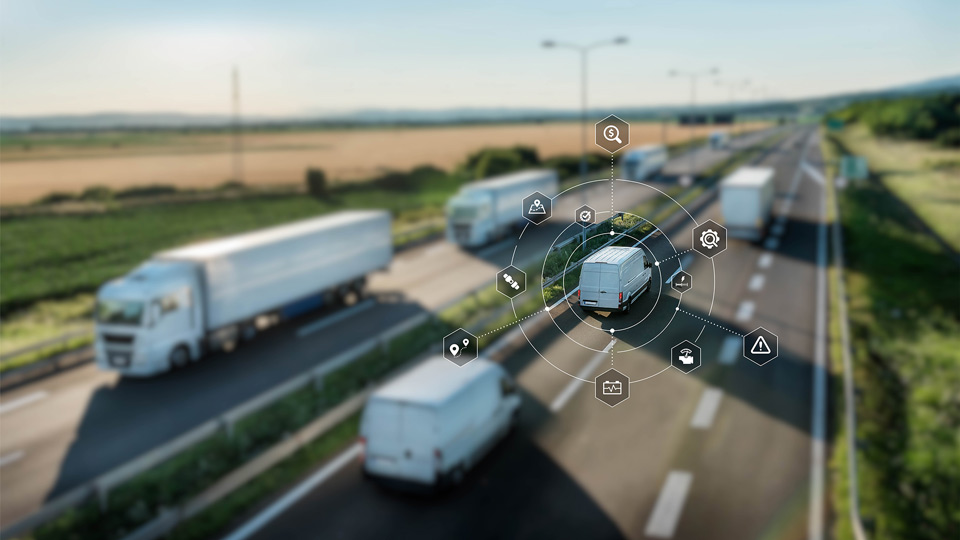
Putting fleet data quality to the test for risk management
March 25, 2022
.jpg)
Customizing mobile workflow and fleet management to better serve drivers
June 5, 2020
.jpg)
Overview of NOM-012 weights and measures regulations for Mexico what they mean
October 1, 2018