Quality assurance testing vehicle GPS devices: how it works
How Geotab uses Big Data and advanced analytics to optimize operations and maintain high quality standards for our Geotab GO7 gps vehicle tracking devices.
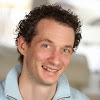
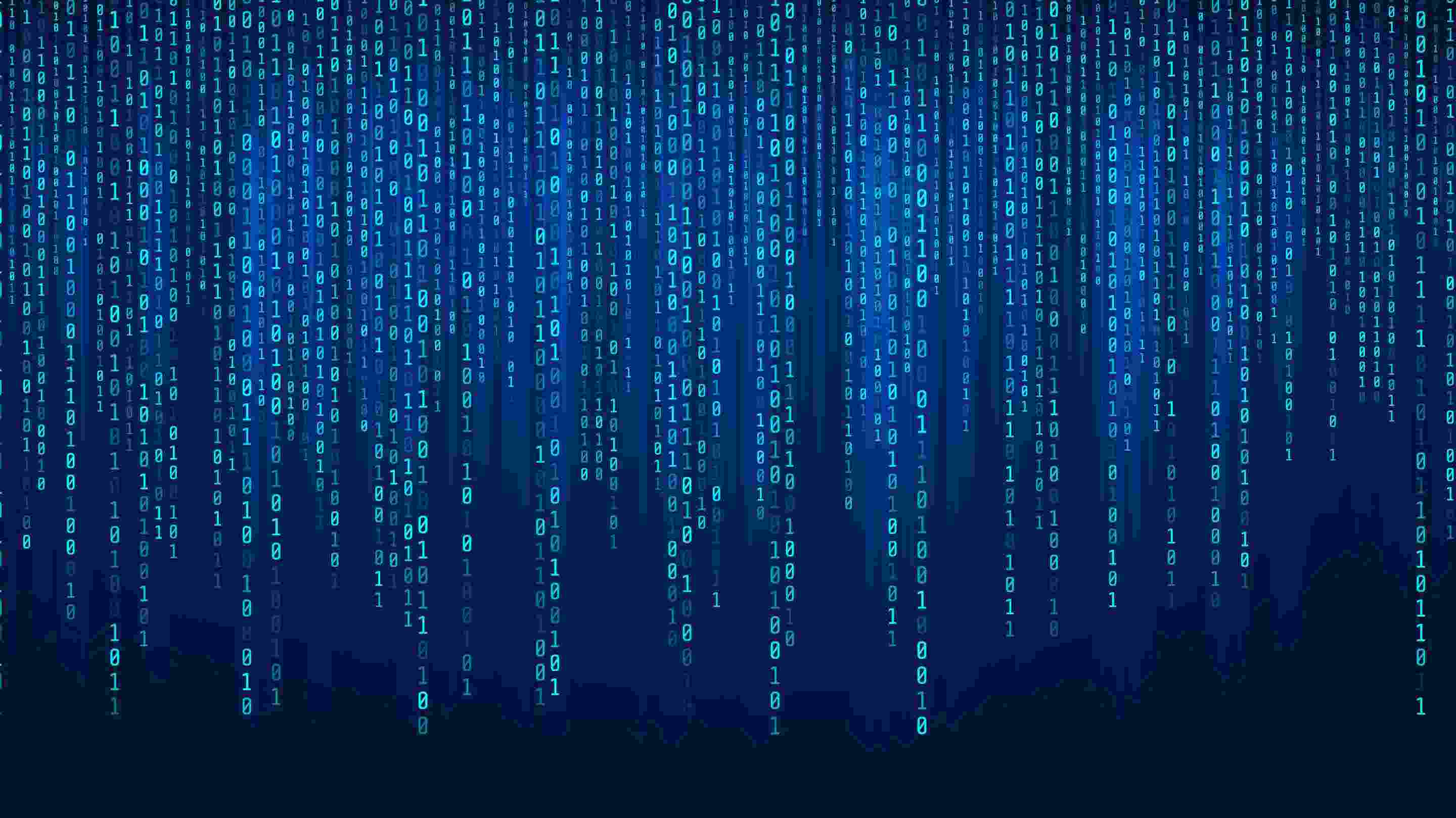
At Geotab, we aim to follow our company slogan “Management by Measurement” in every part of our business, and this includes production. Quality assurance testing vehicle gps devices is an ongoing exercise in analytics and technology innovation.
Geotab leverages the power of Big Data and advanced analytics to optimize operations, like other leading-edge manufacturers. We use real-time data to monitor quality as the product moves from the suppliers all the way to the final customer. If there is an issue with any unit, we are armed to respond quickly and take the right type of corrective action. As a result of this diligent monitoring,
Geotab has an extremely low in-warranty field failure rate for the Geotab GO7 gps vehicle tracking device.
Suggested Reading: Device Testing: What It Means for You and Your Business
Geotab — Quality Control From Start to Finish
All of Geotab’s gps vehicle tracking devices are checked with product testing machines designed by our in-house engineers. These testers record every detail of every unit that they inspect. On a typical day, this data may contain over 40,000 cells of information that we can analyze and use to regulate and monitor various aspects of the supply.
On the supplier side, Geotab looks at the following:
- Supplier testing process: what they test and how often. Are they building what is required based on forecasting and our demand pulls?
- Pass rate: The amount of unique ID serial numbers that pass for a set time period.
- Fail rate: The amount of unique ID serial numbers that fail for a set time period.
- Fault codes: The fault codes associated with the failed unique ID serial numbers.
- Average cycle time for testers.
- Total number of tests: The number of times units are tested before they pass.
The information collected on supply and production is pumped into Geotab’s Big Data system for analysis. The results paint a picture of what is happening at each supplier, including internal testing.
Having this data allows us to pinpoint issues if and where they occur. For example, extra cycle times may indicate potential tester issues or process-related problems. The amount of passed versus failed boards tells us about the efficiency of the process and supplier scrap rates. Fault codes help us identify issues in processes, supplier components, or with testers.
A few examples of charts we use include:
- Supplier Pass versus Fail + cycle time by date and product code
- Supplier fault analysis by product code
- Overall scrap rate
Read this Automotive Fleet interview to find out how fleet manager’s can use analytics to improve fleet safety.
In the Field Product Quality
Monitoring data about customer returns is a very important part of the overall quality of Geotab’s telematics product. It allows us to understand issues related not only to the process, but to potential engineering or even sim account issues. Geotab is able to isolate all kinds of trends to identify if there are issues with training or installation. The scope of analysis is broader with product returns.
Making sense of the data and providing feedback to the designers is critical to the continual improvement of Geotab’s high-quality telematics technology.
Geotab takes a rigorous approach in reviewing returned merchandise. A thorough returned goods process is carried out before root cause analysis is started:
Summary of Geotab Returned Goods Process:
- Case is reviewed to understand the issue.
- Unit is physically inspected for damage or tampering.
- Unit is powered up and information is analyzed.
- Unit is run through production testers.
- Detailed circuit analysis is performed to isolate any identified issues such as a component malfunction.
- If no evidence of issues persist, unit is powered up for extended lengths to determine if there are intermittent related issues.
Pinpointing Trends With Big Data
Using all this information, we classify the failures into 13 general categories, ranging from Global Positioning System (GPS) or Global
System for Mobile Communication (GSM), to process, firmware, or sim-related. These categories allow us to identify trends in the returns and ensure we are taking care of problems before they escalate.
From there, we break down the root cause further into a number of secondary categories. This data analysis allows Geotab to pinpoint trends in high-resolution and make specific changes to rectify the exact issues that are causing any product returns.
We track trends on the quality of our Geotab telematics device products on a monthly basis over many years and product types to understand how we are progressing towards our quality improvement goals.
Geotab takes the quality of our products very seriously, so we can continue to provide the best-available telematics technology to market. We pride ourselves on being upfront, vigilant, and responsible for our product. Every issue is given close attention and consideration. By using the data collected, Geotab can prioritize and address issues quickly. Most importantly, we continually learn from these issues and every day we are making our product better for you.
Subscribe to get industry tips and insights
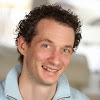
Marc Christelis is a Production and Quality Manager for Geotab.
Table of Contents
Subscribe to get industry tips and insights
Related posts
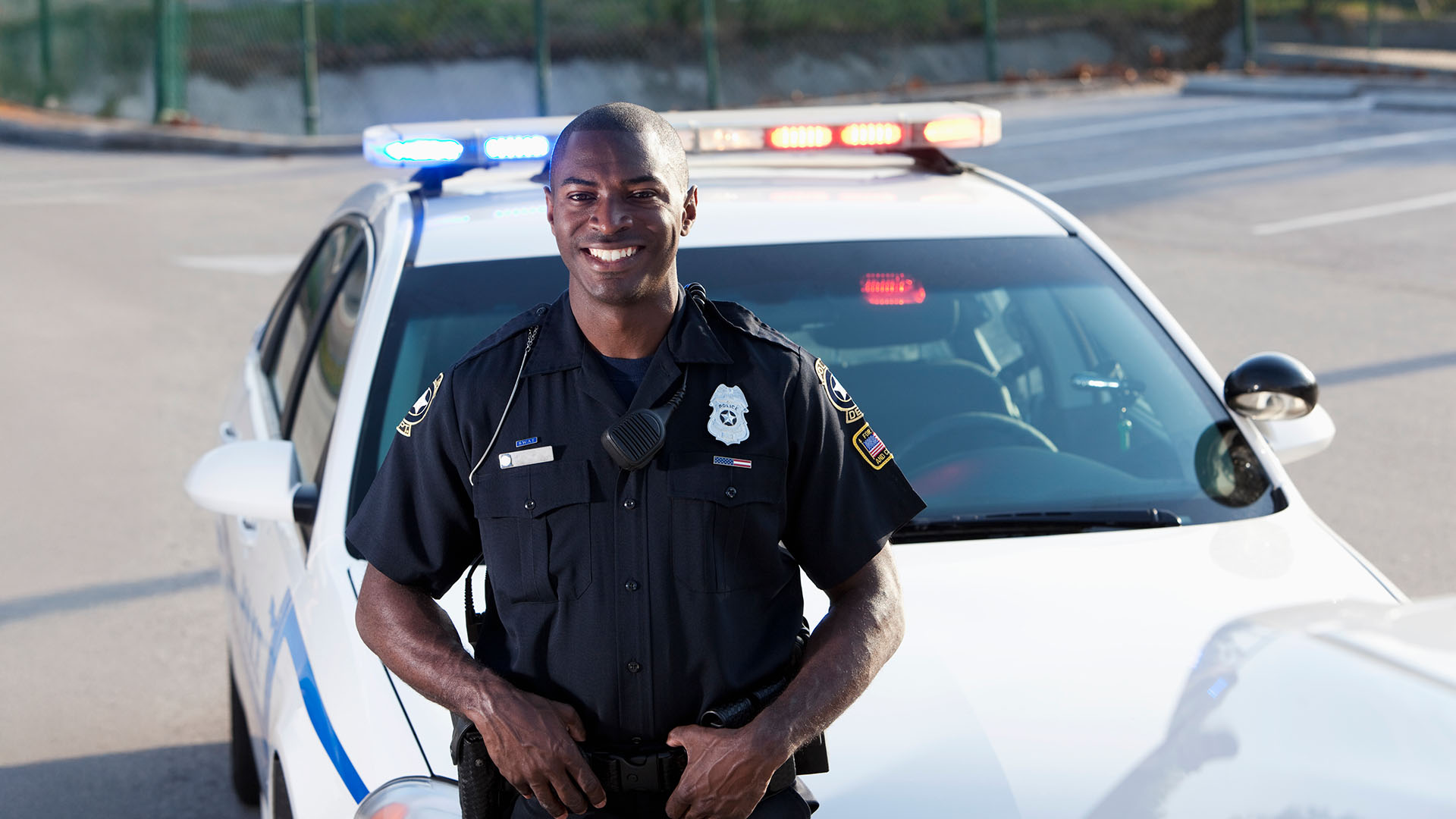
The impact of unproductive idling on police vehicle service life
June 10, 2025
3 minute read
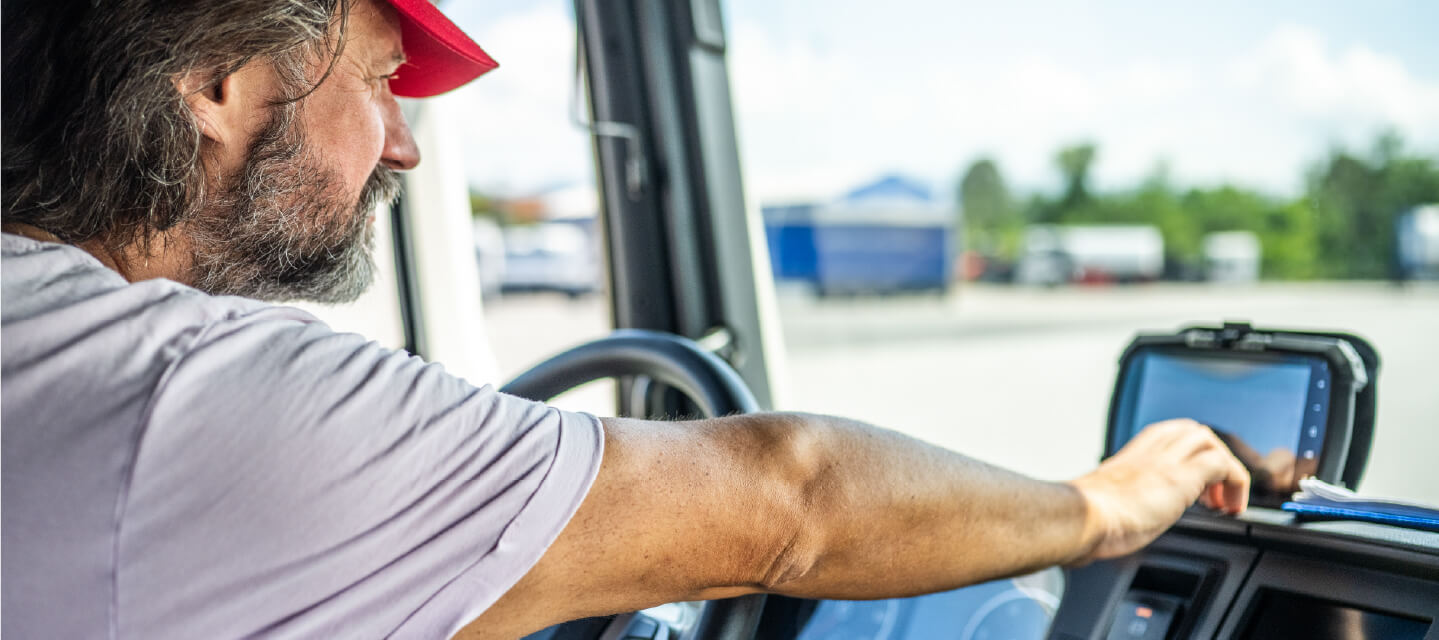
Multi-stop route planners: A fleet manager's guide + best tools in 2025
June 5, 2025
5 minute read
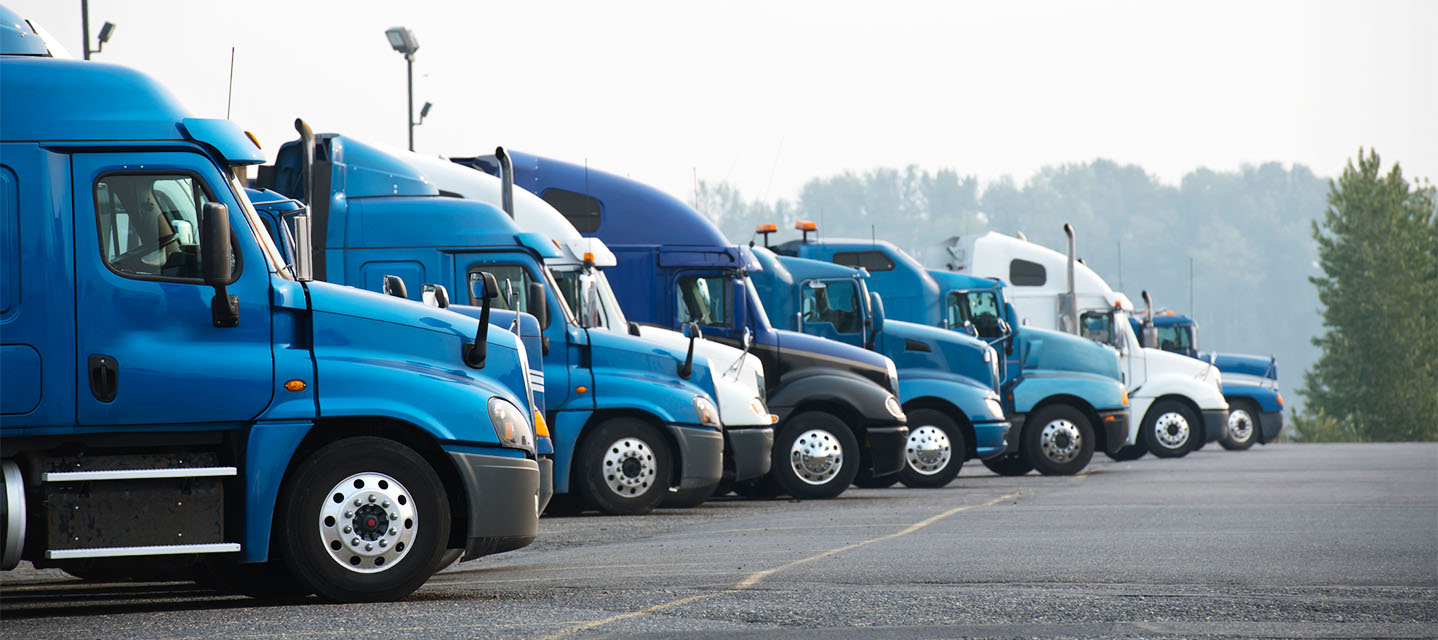
Commercial truck insurance cost: Rates by state + how to save
June 5, 2025
5 minute read

The ROI of telematics for truck lessors: Turn data into profit
May 27, 2025
3 minute read