Field service foresight: How telematics boosts predictive power
Discover how telematics transforms field service fleets from reactive to predictive. By leveraging Geotab data, companies can anticipate maintenance, optimize operations, and enhance driver safety, leading to improved efficiency and customer satisfaction.
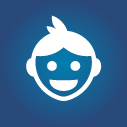
By Geotab Team
Jul 25, 2025
.jpg)
Key Insights
- Learn how telematics fleet data is at the core of shifting fleet management from reactive to predictive
- See how fleet telematics can provide a clear picture for fleet management that leads to better outcomes for resources, customers and driver safety
Traditionally, field service companies have been stuck in a reactive mode, responding to fleet issues and customers without the ability to predict or better manage their operations. This approach leaves fleet service managers and technicians to constantly juggle competing priorities like urgent customer calls, unforeseen traffic and unexpected downtime. This not only diminishes customer satisfaction and leads to wasted efforts and rising fuel costs, but it also overlooks the immense potential for field service fleet operations to become strategic and data-driven.
Artificial intelligence (AI) and its predictive capabilities are profoundly changing how field service companies can manage their businesses. As highlighted at the Field Service Palm Springs 2025 conference, many leading companies are already leveraging their own field service data and employing field control analytics to revolutionize their operations. By harnessing their own data, they can now conduct predictive maintenance, optimize labor usage and safety protocols, analyze unstructured information and forecast inventory levels with unprecedented accuracy, effectively transforming service fleet management for the better.
Fueling predictive maintenance for your fleet
This is where field service data, driven by telematics makes all the difference. With Geotab, detailed engine diagnostics and fault codes provide early warnings of potential mechanical issues, allowing for proactive repairs before they escalate into costly breakdowns. Tracking precise mileage optimizes service intervals and predicts component wear, while operating hours give insight into remaining useful life (RUL) metrics, like equipment utilization and lifespan.
Analyzing driving patterns also becomes possible. From harsh braking, rapid acceleration to excessive idling—telematics data provides performance trends that impact fuel efficiency and driver behavior, preventing early vehicle wear or potential safety incidents. All this integrated information forms the foundational field service data needed to create robust predictive models. This proactive approach ensures businesses are better able to meet customer demands, eliminating the fear of unexpected costly breakdowns and downtime.
A compelling real-world example of these advantages comes from JJM Mechanical Group, who significantly improved their operations by adopting Geotab's telematics solution. By partnering with Geotab, the company was able to obtain real-time vehicle tracking, leading to more accurate customer ETAs and efficient dispatching of technicians for urgent calls. The implementation also boosted safety, resulting in a 24% reduction in harsh driving events and a 66% increase in seatbelt usage. Furthermore, proactive maintenance insights from engine data reports minimized vehicle downtime by allowing the company to address issues before they escalated into costly breakdowns, while also facilitating the swift recovery of a stolen vehicle.
Anticipating failure: The role of telematics in predicting vehicle needs
The ability to foresee potential issues in fleet service vehicles is a significant value-add for predictive analytics, particularly as fleet service managers and business leaders aim to maximize fleet uptime and operational lifespan. By leveraging historical patterns of vehicle lifespan, derived from this rich telematics data, field service business leaders can inform strategic purchasing decisions, and field service managers can schedule maintenance proactively, preventing failures.
Moving to a predictive business model was a game-changer for Interstate Batteries. By deploying Geotab, the company could monitor engine fault codes and anticipate repairs before they occurred, with notifications sent directly to the fleet manager. This shift not only led to a 10% reduction in maintenance costs but also eliminated the need to wait for vehicles to break down, leveraging real-time mileage and engine fault codes for proactive care.
The future of field service is data-driven
Ultimately, the old way of reacting to operations is changing. Field service companies are now in a position to use their detailed field service data they get from telematics to completely change how they manage their service fleets. This shift allows for smart predictive maintenance and robust field control analytics, providing clear insights into how things are running. This means their vehicles spend less time in the shop and more time helping customers.
Discover the key findings and more. Download the report.
Subscribe to get industry tips and insights
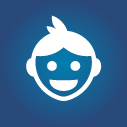
The Geotab Team write about company news.
Table of Contents
Subscribe to get industry tips and insights
Related posts
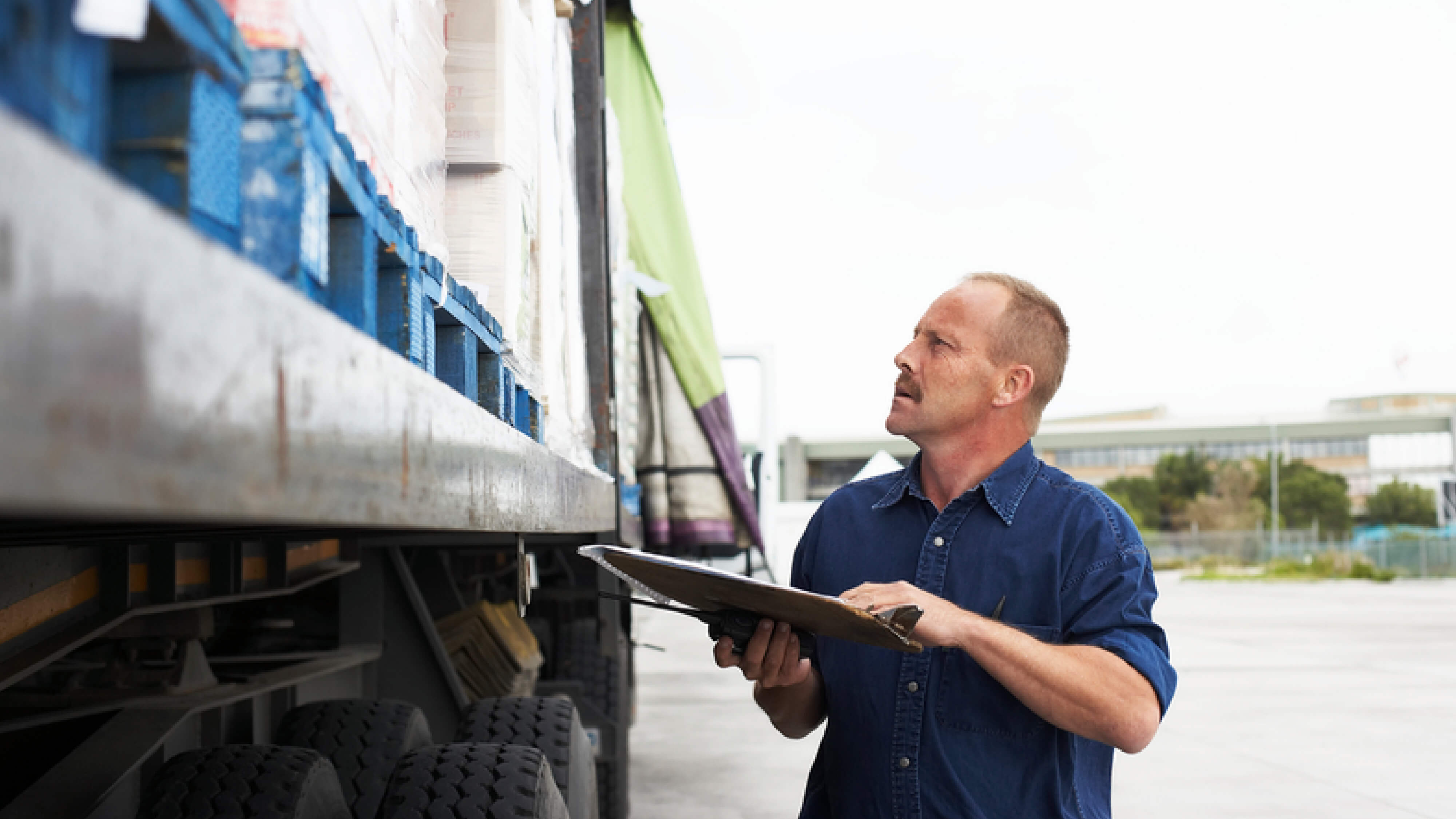
Strengthen high-value cargo security with advanced telematics
August 12, 2025
4 minute read
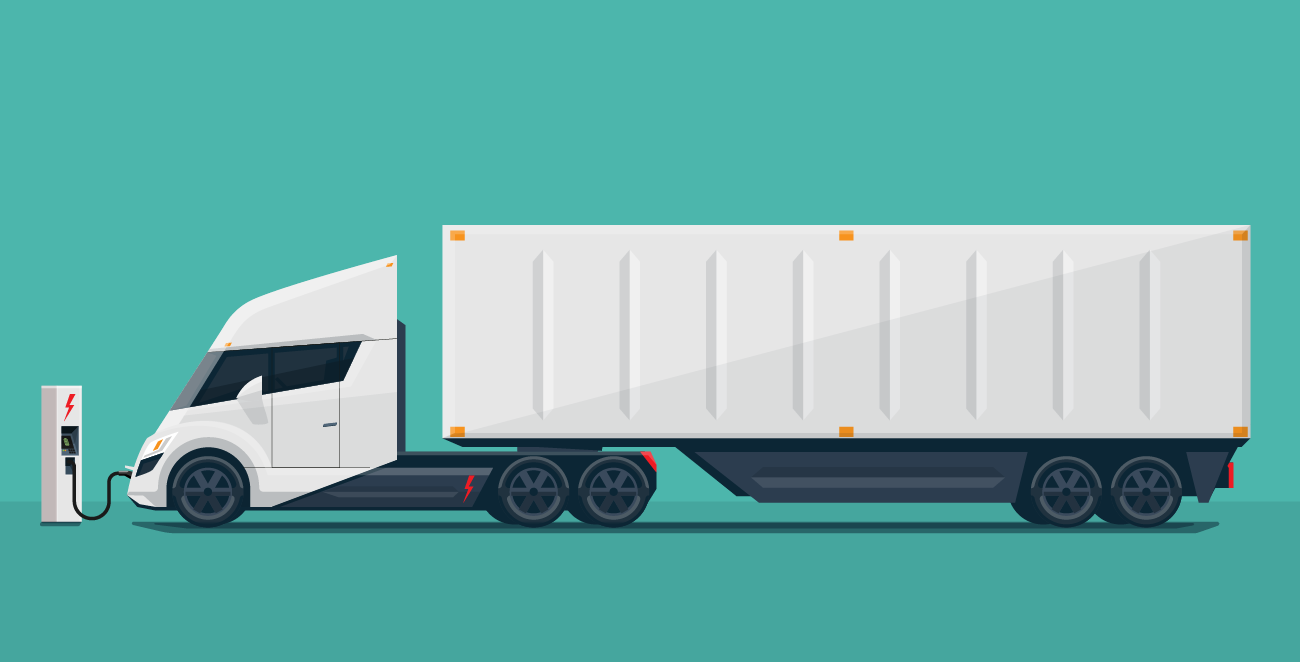
Autonomous trucking: The impact of self-driving trucks in the freight industry + guide
July 30, 2025
6 minute read
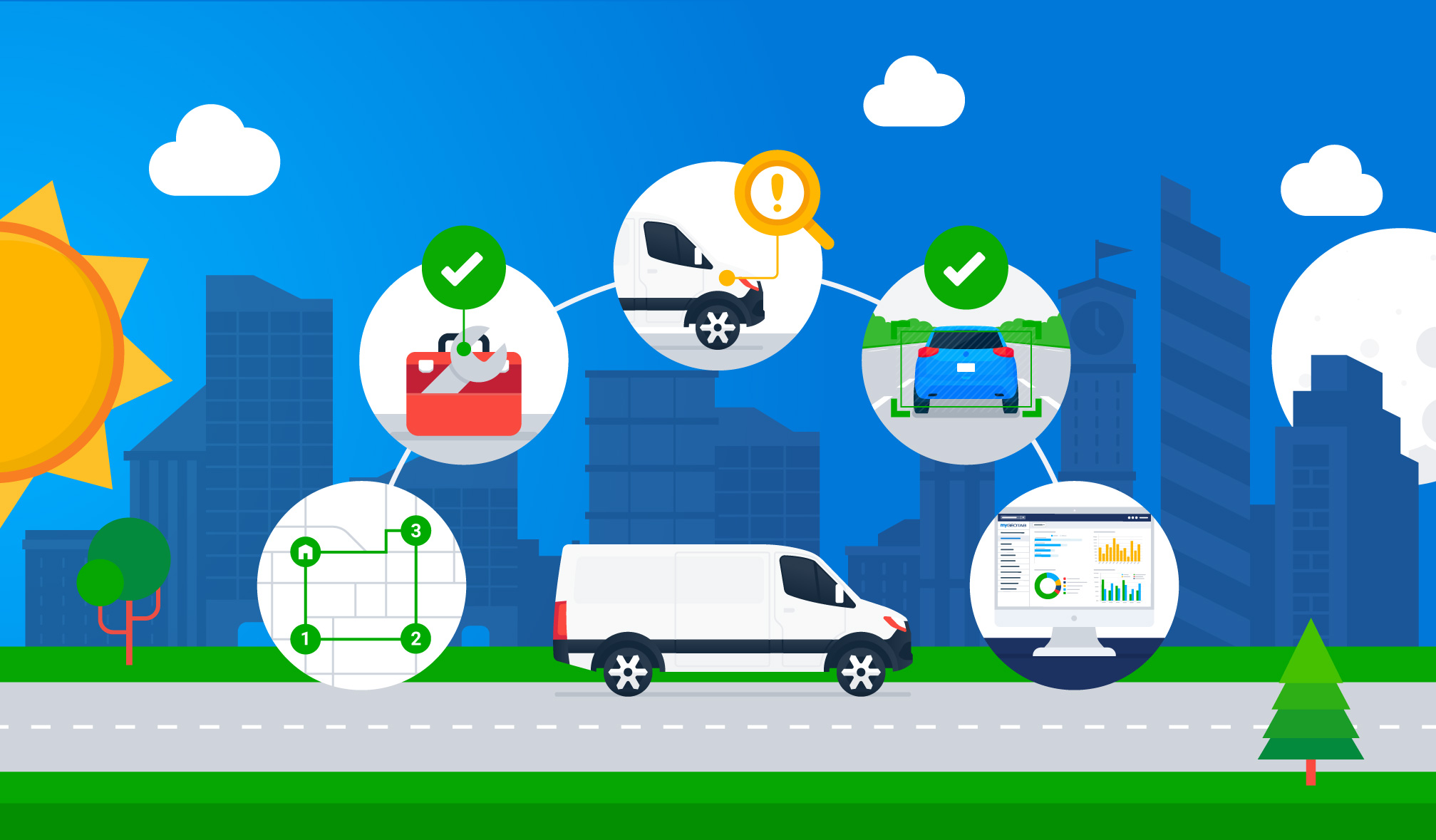
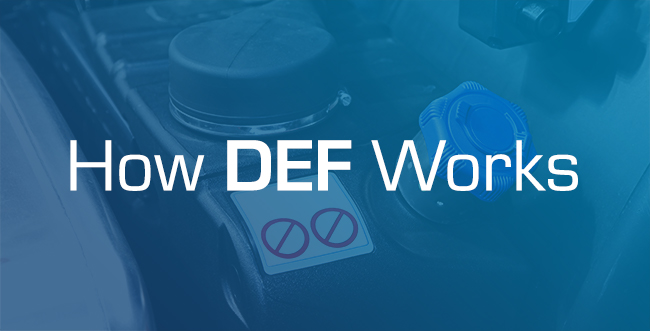
What is DEF? How diesel exhaust fluid works and why it's essential for fleets
July 16, 2025
5 minute read

Odometer reading: How to check + optimize for smarter fleet management
July 15, 2025
5 minute read