5 off-road equipment tracking challenges and how to overcome them
Fleets with off-road equipment are discovering that telematics can help with common challenges like downtime, safety and high fuel costs.
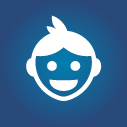
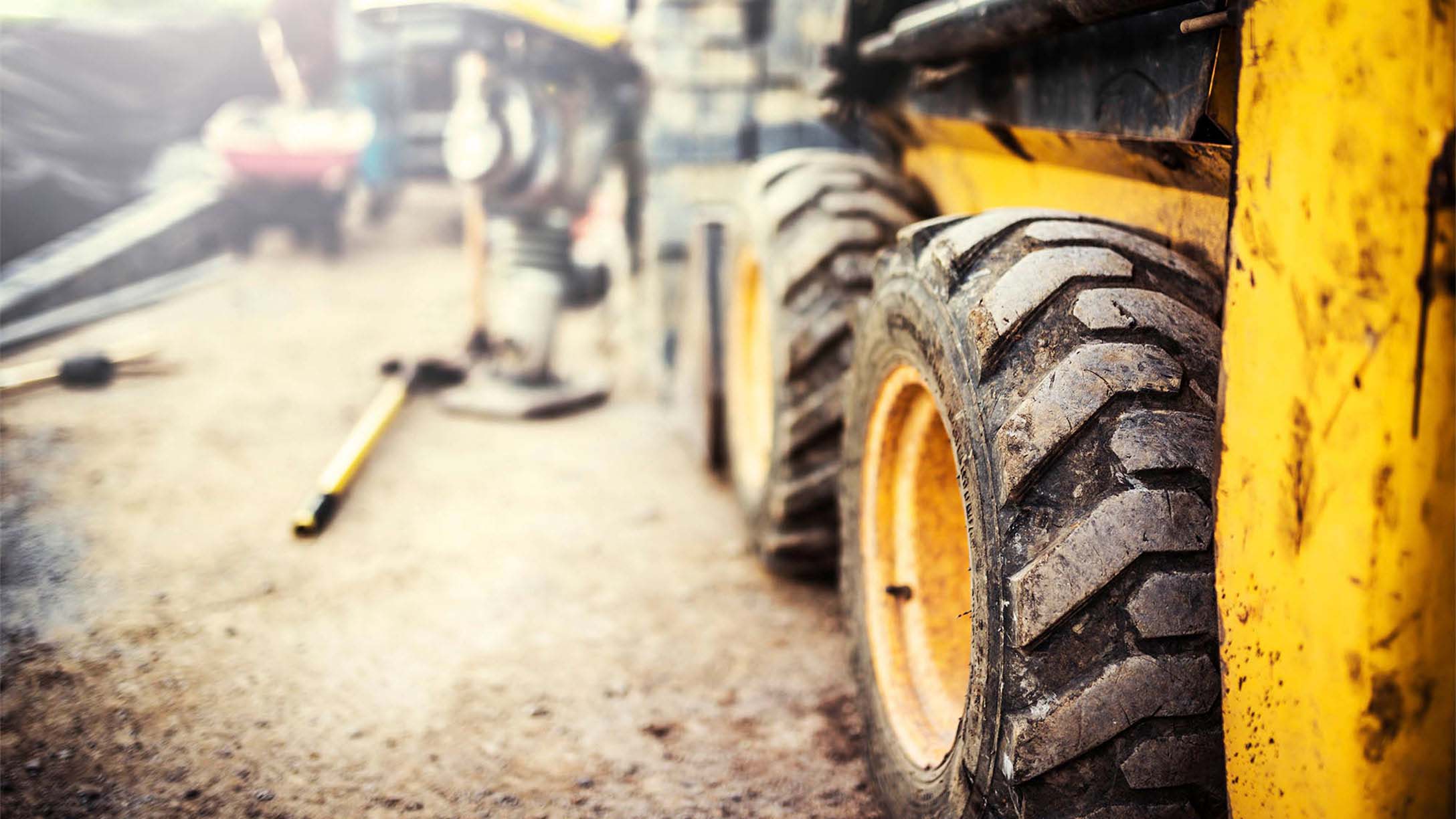
Construction and mining sites are hotbeds for technology, and that includes telematics. Fleets and rental companies with off-road equipment are connecting to telematics for cost management and efficiency benefits.
Telematics can help off-road fleets in several key areas:
- reducing downtime
- controlling fuel costs
- assisting with recovery efforts for stolen equipment
- helping reduce worksite accidents
- reducing the amount of underutilized equipment.
Let’s take a closer look at each of these challenges and how off-road telematics helps.
See also:
Using tracking for cost management in off-road applications
Solving over the road trucking challenges with analytics
Challenge 1: Excessive downtime
Excessive downtime is the number one problem plaguing the construction industry. The unscheduled downtime that occurs when a machine breaks down on the job can be costly. The cost per hour for a road technician is $100 to $150 and this cost does not include lost productivity to the fleet when a piece of equipment breaks down.
Solution: Monitor operations with GPS tracking
Connecting Geotab’s GO RUGGED device allows you to monitor the health of a piece of equipment. Based on engine data and diagnostic trouble codes, you can spot a developing problem and take action to get it repaired before a catastrophic failure occurs. Knowing in advance what the problem is also means the technician can arrive on site with the proper tools and parts, which can also minimize dreaded downtime.
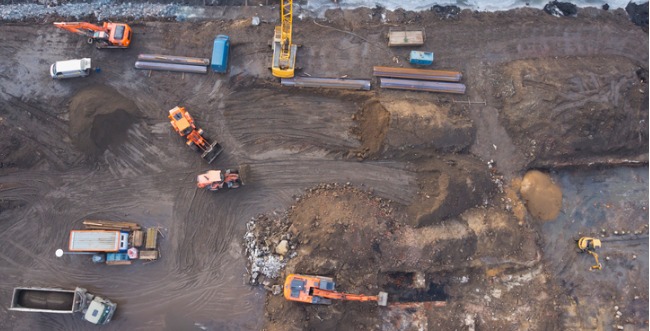
Challenge 2: High fuel costs
Fuel is one of the biggest expenses a construction operation faces. Even with the lower fuel prices we are seeing today, idling equipment unnecessarily wastes fuel, puts an extra load on the engine and contributes greenhouse gas emissions.
Solution: Track idle time and fuel use
GO RUGGED lets you see how much time a piece of equipment is idling. You can use the device to set alerts when the equipment is idling outside of your preferred time limit. While it is impossible to reduce all idling, using GO RUGGED allows you keep it to a minimum.
See also: Learn how to cut maintenance costs with Flex’s TT600 series solar powered asset tracker. For more details, go to Solar Asset Tracker on the Geotab Marketplace and click Request Info.
Challenge 3: Stolen off-road equipment
Everyone worries about having their equipment stolen from a job site. Any type of theft impacts operations, whether it’s a dozer or excavator costing $100,000 or a $5000 air compressor or small generator. When a piece of equipment goes missing, productivity suffers.
Solution: Quick location updates
Geotab provides active location tracking of equipment, and because of its quick reporting capability, you’ll know sooner when a piece of equipment is not where it is supposed to be. The map in MyGeotab allows you to see the exact location of the equipment, which can help speed the recovery of the equipment. Automatic triggers can be set that will send a notification if the equipment is moved off the site.
Challenge 4: Work site collisions
While it can be hard to predict incidents on the site, telematics data can be used to understand what happened.
Solution: Collision reconstruction and in-cab driver/operator coaching
In addition to location tracking, telematics has added benefits like collision reconstruction. With Geotab for example, a fleet manager can verify events by reviewing the trips history, accident and log data, speed profile, and the accelerometer and RPM graphs. The data can also be used to help train equipment operators on safe equipment operating practices.
Fleets can also proactively manage safety with technology like GO TALK. This in-cab verbal coaching solutions delivers verbal feedback to drivers based on predetermined safety rules.
Challenge 5: Underused equipment
Underused equipment is a drag on profitability. Having too much equipment or the wrong mix of equipment can be costly. On the other hand, using some equipment too much impacts maintenance.
Solution: Telematics reports
Geotab allows you to monitor and report on the utilization rate of the entire fleet, making it possible to better disperse the work between various pieces of equipment in your fleet. This prevents some pieces of equipment from being over utilized while others consistently sit idle. This data also helps you right size your fleet so that you have enough of the right kinds of equipment to complete the projects you typically have.
Subscribe to the Geotab newsletter to have stories like these delivered to your inbox.
Related:
Subscribe to get industry tips and insights
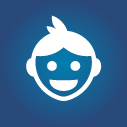
The Geotab Team write about company news.
Table of Contents
Subscribe to get industry tips and insights
Related posts
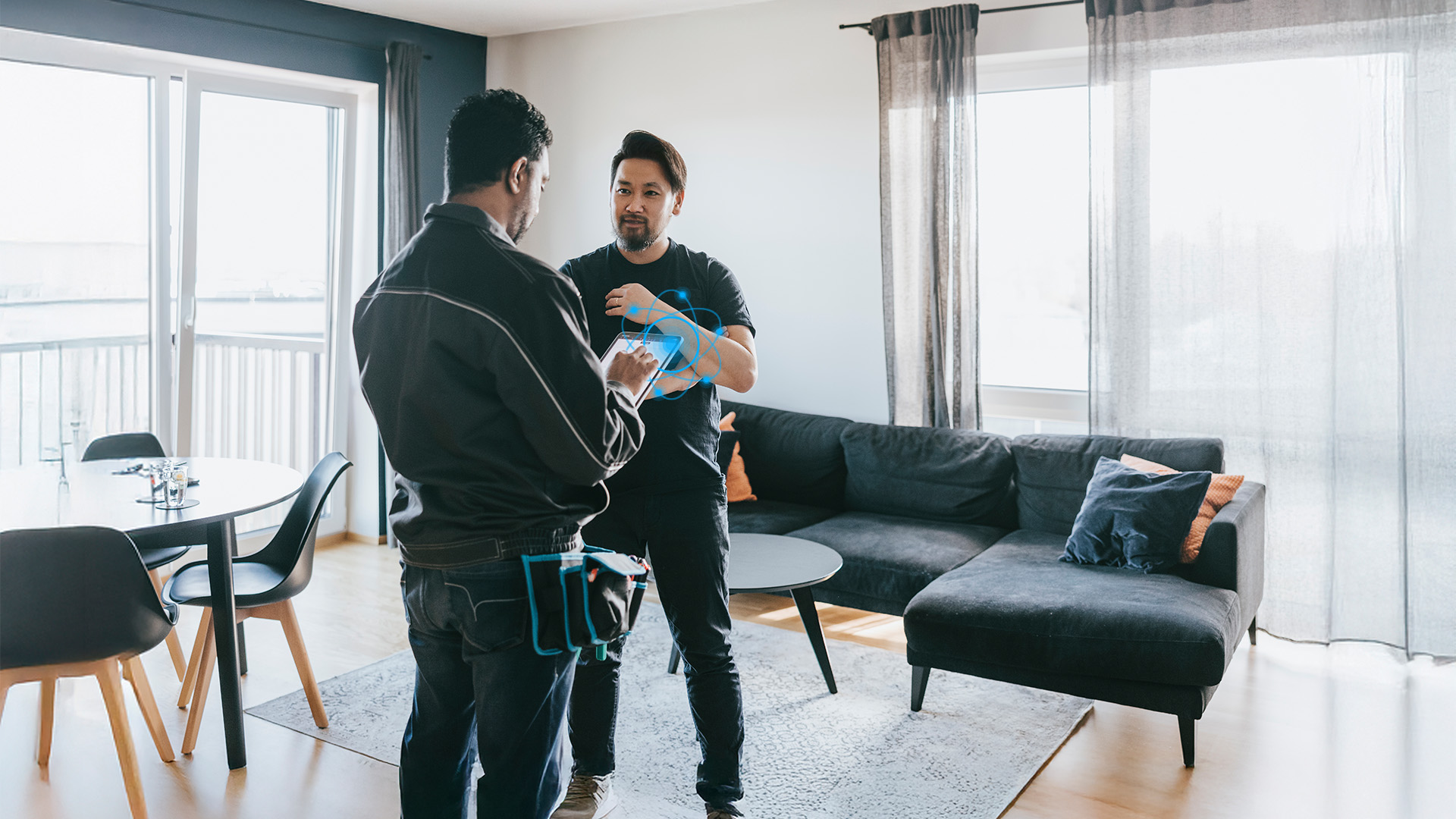
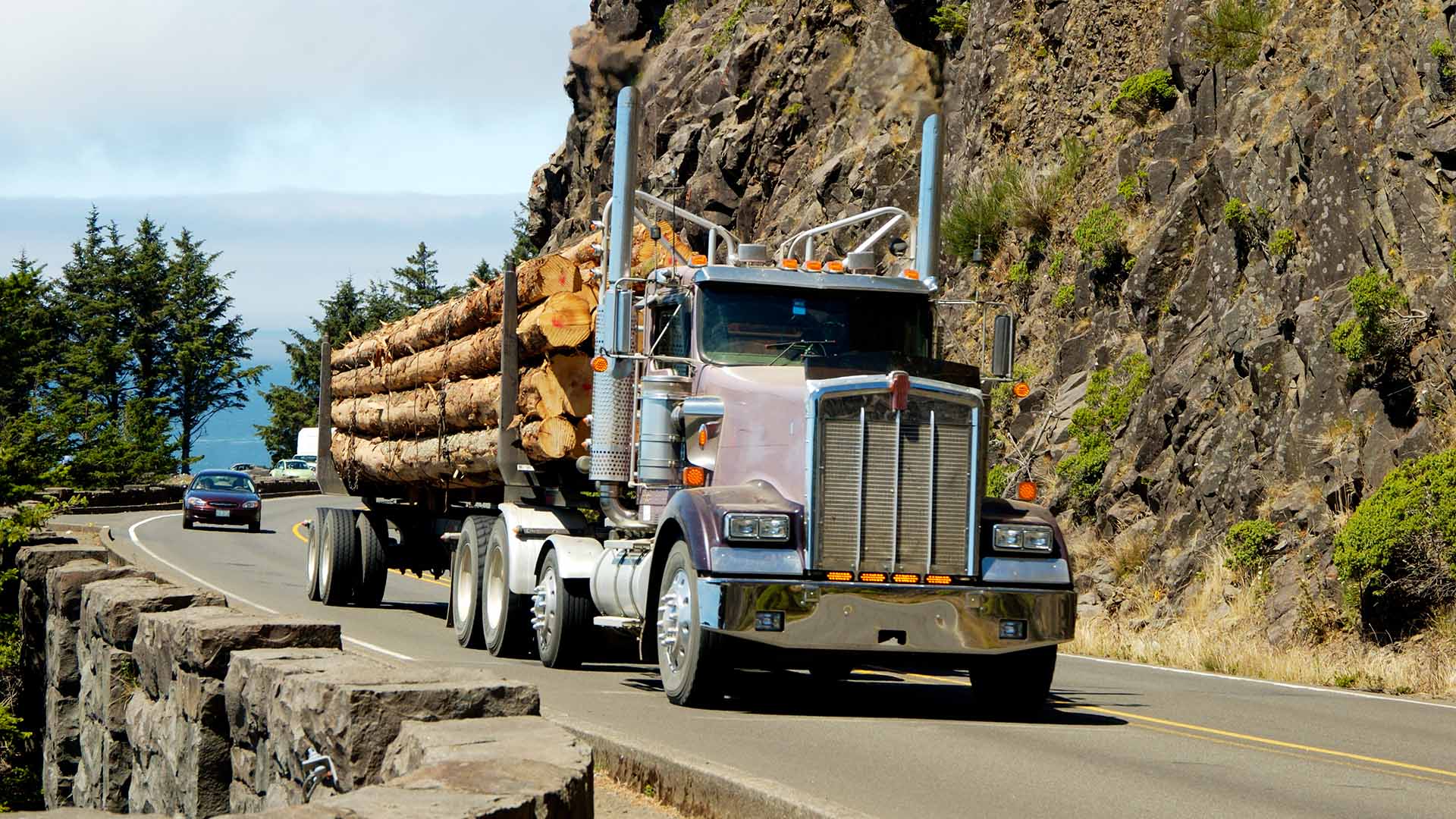
Fuel efficiency techniques every truckload carrier should know
May 30, 2025
3 minute read
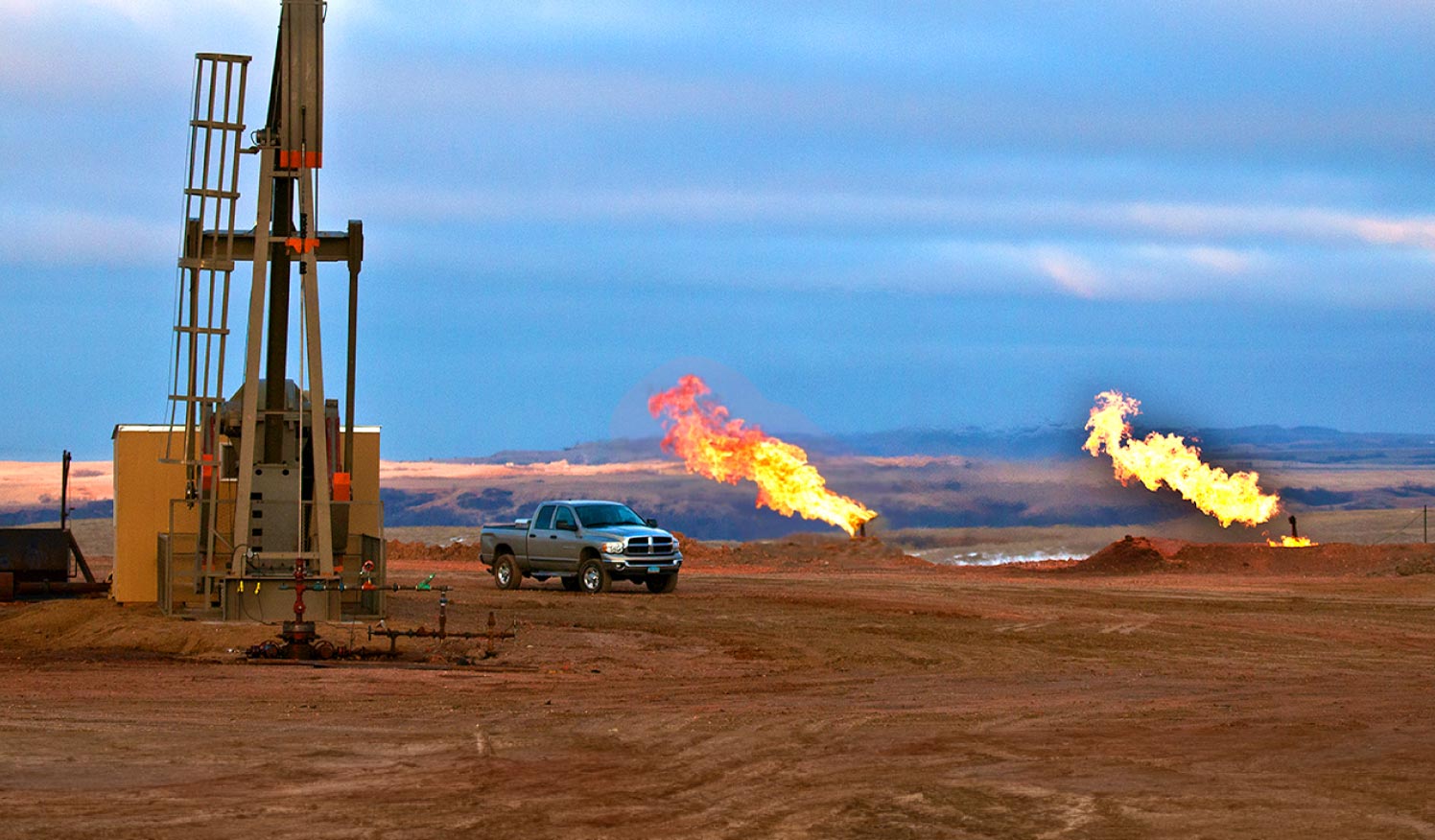
5 data-driven strategies to optimize your oil and gas fleet
May 29, 2025
2 minute read
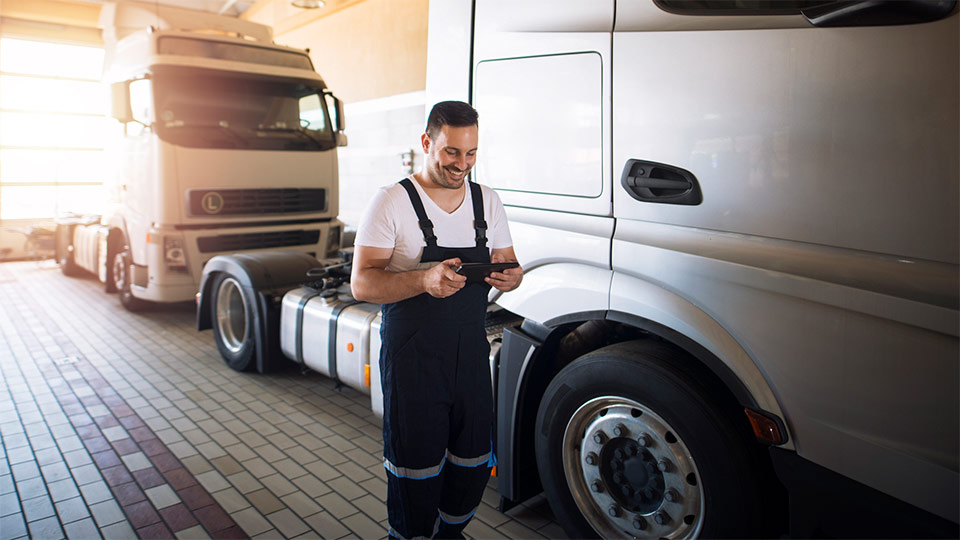
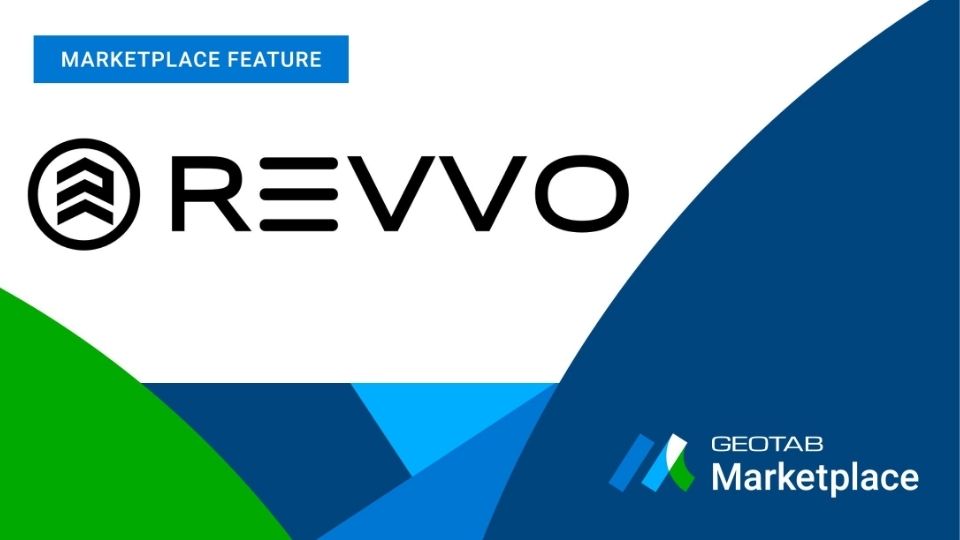
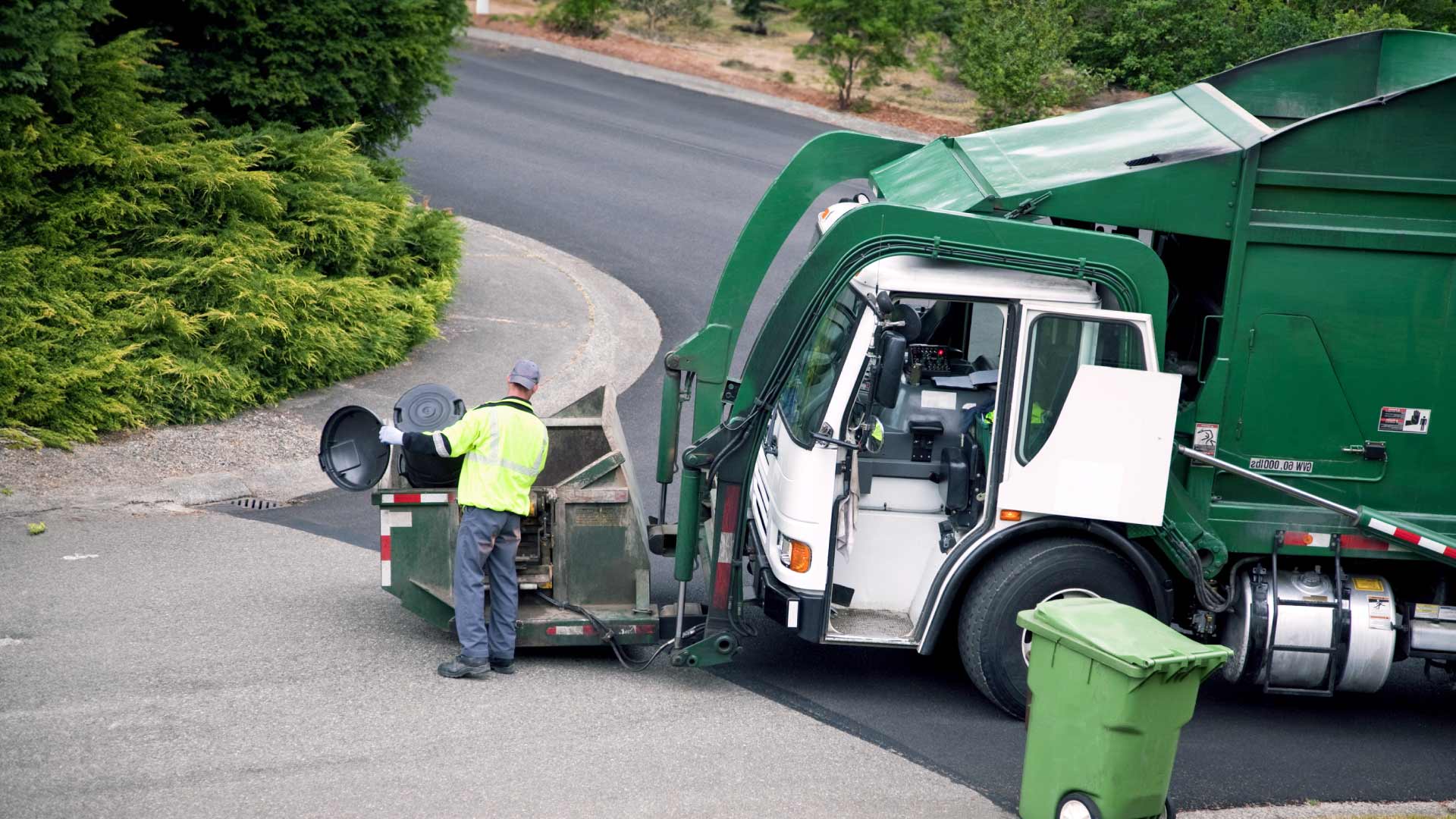
Six ways telematics reduces costs for waste management fleets
May 16, 2025
6 minute read